I also picked up some poplar for a scabbard project, but that will be a different post. Right now, the core is drying in my dad's garage.
I pulled off the old grip and risers. There was alot of glue/dye residue on the grip core, so I gave it a quick smoothing with a sanding block. I figured that I would be trying this a few times, so I left some residue in place and did not reshape the core from its stock hexagonal appearance.
I then cut risers from leather latigo and glued them in place with Elmers. Tacking them at the beginning with a tad of Superglue is good to hold them in place so you can pull it tight as you glue them down with Elmers.
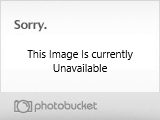
I started my internal cord wrap using thick waxed leather stitching thread. I tacked it down with a drop of Superglue and started spinning...
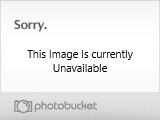
Spinning...I went over the risers on the seam side. If I was doing this for a keeper, I would end and restart at each riser to avoid doing this.
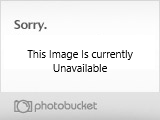
Done...there were some small spaces here and there, but nothing that would be noticed with the finished product.
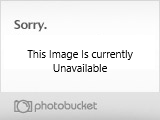
I then wet a piece of 2oz crafting leather the approximate size of the grip...
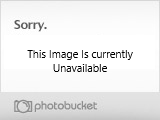
Now, I don't show the next part because my hands were too sticky, but I did the leather just like in the Albion video for the most part. I wet the back with Elmer's white glue, and began molding it around the grip, pressing in the details and getting excess air and glue out. A few times, I had to sort of twist the hole grip to make the seam even. The whole process took around 10 minutes - a little longer than I imagined.
I then wrapped the grip tightly with 550 cord for 4 hours and went to work on my scabbard core some. Then while leaving my core to dry, I came back to the grip and unwrapped it. I used a doe foot to define the risers a little better and push the extra leather into the space between the top and bottom risers.
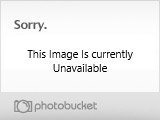
Here is the seam...
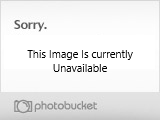
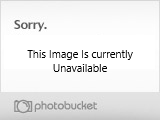
It turned out better than I thought it would on my first attempt. There are several things that I plan on doing different the next time. One is to use taller risers to give them more definition. Two is to do the final drying wrap with a finer material than 550 cord (which I what I happened to have). Three is that when I do this for sure, I will strip and reshape the core - not because I think it will be a problem, but just to do it the proper way.
Other than that, I am pretty happy with my new skill. I'd like to thank all those posting on this topic for the good information in giving guidelines!
EDIT: While I was thinking about it, I went back, slightly damped the leather (which was not 100% dry anyway), and rebound the whole grip with the fine cord I used under the leather. Hopefully, in the morning, I will have a little more detail - then I can call this one done - for now anyway!