Either way, it's cool stuff, right? :)

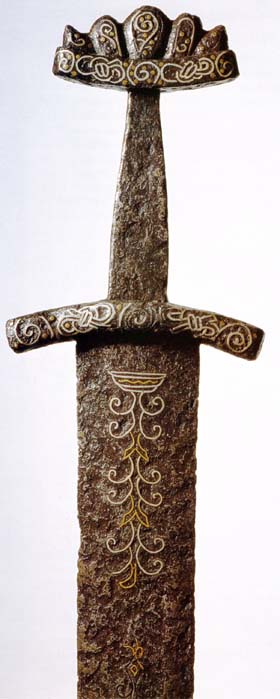
Copyright Peter Finer, 2003

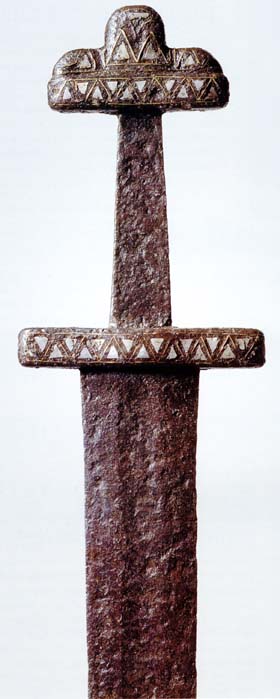
Copyright Peter Finer, 2003

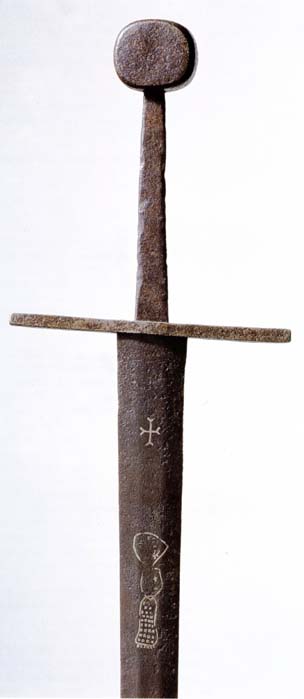
Copyright Peter Finer, 2003
Hessink's Veilingen wrote: |
An Extremely Rare German Sword of Justice from the Town of Celle, dated 1643.
Cross shaped hilt and large pear shaped facetted pommel. The superb double-edged blade etched with foliage and strapwork and copper inlaid wheel and rope. The wide single fuller is engraved with an inscription related to the function of the sword: 'When I Raise This Sword - I Wish The Sinner The Eternal Life'. On the back engraved in the fuller 'CLEMENS HORN ME FECIT SOLINGEN' and stamped with a unicorn mark surrounded by a text reading 'CLEMENS HORN FIDE SED CVI VIDE', and copper inlaid city arms of Celle. Leather covered hilt. Length 118.5 cm. Note: Swords of this type, known as executioner's swords, always are of very high quality, made by the best of blademakers. |
Jonathan Atkin wrote: |
guess abit off topic but how would one go about getting inlay done on your pride and joy of your collection? |
Chris Fields wrote: |
Wow, that executioner sword is quite amazing.
I have done some inlay before, but it was with bronze in steel. You can tig weld bronze and it will flow right into the grooves cut into the steel and stick like it's one piece. I haven't done that in a long while though since the only tig welder I had access to was the university of south florida, and I graduated back in 05. I believe you can braze copper and brass about the same way though. Historically I believe alot of it was chiseled and cold worked in. |
Tim Lison wrote: |
Kjell-
Great pic! Do you have any more like it? If yes, please post them!!!! |