I am starting a thread to share my various noodling around in the shop projects that have anything to do with arms and armor. my intent is not necessarily to show "hey look at the monster I have created" but rather to get feedback of a more critical nature such as "stop stop what you are doing and get yourself the proper tool before you hurt yourself" or "go to the store and get this wiz bang product and all of your troubles will be gone" or "Thom, why are you doing it the hard way - just do this instead you fool!"
although positive feedback is always welcome too :D
I have already shown a few of these projects like the rehafting of the cold steel poleaxe and the scabbards I have done and the ATrim sword re-hilts.
Lately I have been fooling around with butted mail. I bought a couple of pounds of "shop sweepings" from the Ring Lord on the cheap and have been having fun with these rings. The shop sweepings came in a variety of sizes so the first job was to sort out the various rings and put them into individual bags:
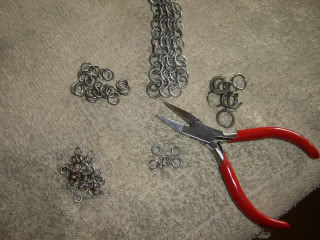
Its a mixed bag of ring sizes and type. But there was a fair amount of mild steel 16 gauge/5/16" and 14 gauge/1/4". Some bigger stuff and some smaller stuff. I started weaving some 4:1 with both and then mastered a 6:1 weave using a combination of steel and copper+bronze rings. I thought about a couple of ideas of what I could make with this stuff and then it dawned on me that a mail standard would be a fun project. So I have been making a butted mail standard with the rings. So far I have made a couple of long 6:1 strands with the 5/16th rings and am knitting them together with the smaller 1/4 inch rings in a 4:1 pattern. I am thinking that I have enough rings for 3 or 4 strands 22-24 inches long. the 6:1 weave is actually pretty tuff stuff despite being butted (If I have some left over I think I will lay some out on a straw bale in the back and shoot at it with my compound bow with a target point just to see what happens). since a standard's function around the neck is mostly to protect against glancing cuts I think rings woven at 6:1 will produce a rather functional piece of armor even though its butted. you can see the difference between the classic 4:1 (above) and the strands of 6:1 (below) - I wonder if this isn't what you sometimes see referred to as "double mail" in some historic commentary. its a much denser weave
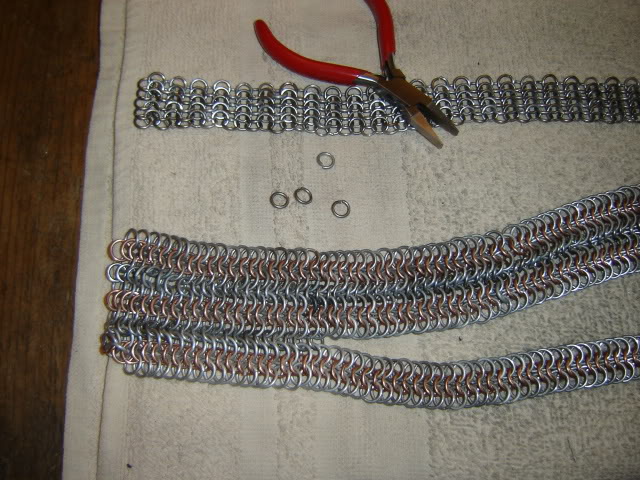
The learning curve has included a number of gashes on my bare hands from slip ups while closing rings as some of these rings are pretty tuff - not all of it is mild steel. But certainly the spring loaded pliers are a big help when doing butted mail. I find it best to work in small batches - opening up 20-30 rings at a time and laying them out carefully in my immediate work area such that they don't entangle with each other. That allows me to to pick up them up efficiently with pliers for weaving such that I don't constantly have to put the pliers down. Any comments on the size of mail standards is certainly welcome and I am interested in weaving techniques other people are using as I am finding this to be a rather addicting fun, at least in 20-40 minute long work periods. beyond that it starts getting tedious, for me anyway..........